Özyeğin Üniversitesi, Çekmeköy Kampüsü Nişantepe Mahallesi Orman Sokak 34794 Çekmeköy İstanbul
Telefon : +90 (216) 564 90 00
Fax : +90 (216) 564 99 99
info@ozyegin.edu.tr
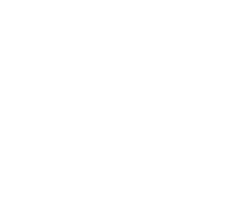
Thesis Defense - Çağatay Emre Ayhan (MSME)
Çağatay Emre Ayhan - B.Sc. Mechanical Engineering
Asst. Prof. Altuğ M. Başol– Advisor
Date: 13.01.2020
Time: 10:00 – 11:00
Location: This meeting will be held ONLINE. Please send an e-mail to gizem.bakir@ozyegin.edu.tr in order to participate in this defense.
Thermal Underhood Analysis of a Heavy Commercial Vehicle using open source CFD package OpenFOAM
Thesis Committee:
Asst. Prof. Altuğ Melik Başol, Özyeğin University
Asst. Prof. Özgür Ertunç, Özyeğin University
Asst. Prof. Ayşe Gül Güngör, İstanbul Technical University
Abstract:
Underhood thermal design of heavy commercial vehicles has a large influence on the performance and reliability of the vehicles. Thermal design of the underhood compartment is a challenging task with many constraints and design parameters. Designers can benefit from the numerical tools that are capable of predicting the thermal conditions inside the underhood area both accurately and fast. In this thesis, a numerical model for the underhood thermal analysis of a heavy commercial vehicle was developed using the open-source software OpenFOAM.
In this study, the capabilities of OpenFOAM has been challenged on the underhood thermal analysis of a heavy commercial vehicle. The mesh generator snappyHexMesh performed fairly well in the meshing of the complex geometries with reasonable resolution and quality. The buoyantSimpleFoam solver was used with the heat exchanger, rotating fan, and heat shield models. The radiation heat transfer within the underhood area was modeled using the surface-to-surface radiation model. The turbocharger heat shield temperature predicted with the solver matches reasonably well with the measurements with discrepancies less than 10⁰C. Overall, the computational study took around 38 h running the solver on 56 CPU cores. Except for the radiation model, the parallel scalability of the solver and the additional models were found to be close to ideal. The radiation model takes about 1/3 of the overall computational time. The computational cost of the radiation model has been evaluated on different cases with varying number of surface elements involved in the radiation calculations. It has been found that the computational cost of the radiation model strongly increases with the number of surface elements. In particular, using the radiation model with more than 20,000 surface elements does not seem to be computationally feasible due to the extreme computational cost of the model. This is partially due to the computational cost inherent to the surface-to-surface radiation model and but it is also due to the lack of parallelization of the surface-to-surface radiation model in OpenFOAM version v1812+.
Bio:
Çağatay Emre Ayhan obtained his bachelor’s degree in mechanical engineering from Bogazici University in 2017. He started the Mechanical Engineering master’s program at Ozyegin University in 2017. He took a part in the project carried out with the partnership of Ozyegin University and Ford Otosan. His main research interest is vehicle underhood thermal analysis.